
ϕ = 0.85 – strength reduction factor for shear according to ACI 349.The available tensile strength of a bolt subjected to combined tension and shear is determined according to the limit states of tension and shear rupture as follows: Combined Tension and shear in bearing type connection The required tensile strength includes any tension resulting from prying action produced by the deformation of the connected parts. The design tensile or shear strength, ϕR n, and the allowable tensile or shear strength, R n/ Ω of a snug-tightened bolt is determined according to the limit states of tension rupture and shear rupture as follows:Ī b – nominal unthreaded body area of bolt or threaded partį n – nominal tensile stress, F nt, or shear stress, F nv, from Table J3.2 Bolts Tensile and shear strength of bolts The bolt resistances are checked according to AISC 360 - Chapter J3. The tensile forces include prying forces. The forces in bolts are determined by finite element analysis. Check of bolts and preloaded bolts according to AISC Accordingly, when Complete Joint Penetration (CJP) groove welds are made with matching-strength filler metal, the strength of a connection is governed or controlled by the base metal and no checks on the weld strength are required. θ – angle of loading measured from the weld longitudinal axis, degreesĪISC Specification Table J2.5 identifies four loading conditions that might be associated with groove welds and shows that the strength of the joint is either controlled by the base metal or that the loads need not be considered in the design of the welds connecting the parts.F EXX – electrode classification number, i.e., minimum specified tensile strength.
#Aisc 14th edition materials code
Ω = 2.00 (Allowable Strength Design, ASD, editable in Code setup)Īvailable strength of welded joints is evaluated according to AISC 360-16 – J2.4 Φ = 0.75 (Load and Resistance Factor Design, LRFD, editable in Code setup) The design strength, ϕR n, and the allowable strength, R n/ Ω, of welded joints are evaluated in the connection weld check. The strength of CJP groove welds is assumed the same as the base metal and is not checked. Check of welds according to AISCįillet welds are checked according to AISC 360 - Chapter J2. The equivalent plastic strain is exceeded at higher stress and the joint does not satisfy anyway.
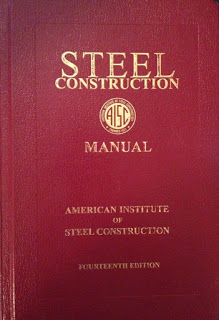
This is not a problem for practical design. The reason is the slight inclination of the plastic branch of the stress-strain diagram, which is used in the analysis to improve the stability of the interaction calculation. The CBFEM method can provide stress a little bit higher than yield strength. The program shows the worst result of all of them. Plate element is divided into 5 layers and elastic/plastic behavior is investigated in each of them.
#Aisc 14th edition materials verification
This value can be modified in Code setup but verification studies were made for this recommended value. The limit value of 5 % is suggested in Eurocode (EN App. When the yield strength (in LRFD multiplied by material resistance factor ϕ = 0.9, in ASD divided by material safety factor Ω = 1.67, which are editable in Code setup) on the bilinear material diagram is reached, the check of the equivalent plastic strain is performed. The resulting equivalent stress (HMH, von Mises) and plastic strain are calculated on plates.
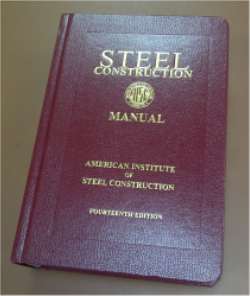

Individual components are checked according to the American Institute of Steel Construction (AISC) 360-16. The stresses and internal forces calculated on the accurate CBFEM model are used in checks of all components. CBFEM method combines the advantages of the general Finite Element Method and standard Component Method.
